Les programmes de maintenance aéronautique : méthodologie de création et cadre réglementaire
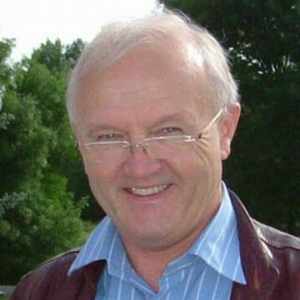
La première règle d’entretien aéronautique fut édictée en 1930 : » les instruments et les équipements devront être révisés à intervalles suffisants pour assurer leur fonctionnement correct à tout moment. »
La méthodologie actuelle repose sur une approche par analyse logique, par examen des conséquences des défaillances fonctionnelles et par un programme d’entretien par tâches.
Ces programmes sont réalisés par un comité directeur à l’échelon de l’industrie entière et appuyé par des groupes de travail spécialisés. Les participants sont des professionnels des compagnies aériennes, des spécialistes des aviations civiles nationales, des ingénieurs du bureau d’étude du constructeur et des fabricants d’équipements et enfin, des spécialistes des programmes de maintenance.
Pour un avion moderne comme l’A340-500/600, cela met en jeu 70 participants, pendant dix-huit mois, et près de quarante-cinq mille heures de travail.
Présentation générale
Un opérateur d’avion de transport est responsable de son programme d’entretien et doit le faire approuver par son aviation civile ; ce programme découle du programme du constructeur (MPD, voir figure 1).
Le MPD du constructeur est la synthèse de trois sources différentes :
• le MRB (Maintenance Review Board), processus principal,
• les règles de certification de type et les exigences opérationnelles,
• la surveillance en exploitation de l’avion, retour d’expérience donnant lieu à des tâches complémentaires spécifiques pour le maintien de la navigabilité de l’avion.
Assurer un niveau de sécurité mondial
Les exigences réglementaires sont établies pour satisfaire le niveau de sécurité établi par l’OACI au niveau mondial.
Chaque pays édicte ses règles de navigabilité, mais les deux plus importantes sont les JAR (Joint Aviation Requirements) établis par les JAA (Joint Aviation Authorities, 33 pays européens) et les FAR (Federal Aviation Regulations) établis par la FAA américaine.
Ces règles de navigabilité portent non seulement sur la conception de l’avion, mais aussi sur les opérations et la maintenance pendant toute la durée de l’exploitation commerciale de l’avion.
Les exigences à respecter intègrent des éléments de la certification de type de l’avion, des instructions pour le maintien de la navigabilité en exploitation (JAR 25 appendice H) et des exigences découlant de la réglementation opérationnelle (JAR OPS 1, JAR OPS 66, JAR 145 et JAR 147).
Les exigences de la certification de type s’assurent que la conception est conforme aux niveaux de sécurité recherchés.
La démonstration de conformité doit être faite avant que le certificat de type ne soit délivré.
Cinq chapitres sont concernés :
• la résistance au dommage et le comportement en fatigue de la structure (JAR 25.571),
• les matériaux utilisés (JAR 25.603),
• l’accessibilité des zones de l’avion (JAR 25.611),
• les équipements, systèmes et leur installation (JAR 25.1309),
• les instructions de maintien de la navigabilité (JAR 25.1529).
Les instructions de maintien de la navigabilité (appendice H des JAR 25) visent à assurer que les instructions et limites de maintenance sont bien établies en relation avec les travaux de la certification de type. Elles doivent être préparées par le constructeur avant la première livraison commerciale.
Elles comportent deux paragraphes importants :
• le paragraphe H 25.3 : a) Manuel de maintenance avion, b) instructions de maintenance, c) à g) portes d’accès, inspections techniques, traitement de protection, fixations structurales, outillages spéciaux,
• le paragraphe 25.4 : limitations de navigabilité, éléments à vie-sûre, ALI et CMR.
Les exigences opérationnelles visent à s’assurer que les caractéristiques inhérentes de fiabilité de l’avion sont maintenues pendant l’exploitation commerciale. Elles sont établies par le pays d’immatriculation de chaque avion.
Elles comprennent 4 sections :
• JAR OPS1, section 1, sub M (pour maintenance),
• JAR 66, personnel de certification (maintenance),
• JAR 145, organisation approuvée de maintenance,
• JAR 147, organisation approuvée de formation à la maintenance.
Le processus général MRB
La réglementation impose l’établissement par le constructeur d’un programme de maintenance.
Les constructeurs ont développé une méthode appelée le MSG‑3 pour développer ce programme et les tâches de maintenance correspondantes.
Le MSG‑3 est l’ultime évolution d’un processus commencé en 1930 par le Transport airline inspection service, ancêtre de la FAA dans son Aeronautical Bulletin 7E section 5 : » Instruments and accessories shall be overhauled at suitable intervals. »
Ce concept restera en vigueur pendant quarante ans. Nous allons voir que d’importants progrès ont été réalisés depuis cette première règle bien limitée.
En 1967, un document de United Airlines résumait les travaux de l’industrie en vue de développer l’utilisation de » Diagrammes de décision pour l’analyse logique des programmes de maintenance « .
En juillet 1969, le processus MSG‑1 (MSG… Maintenance Steering Group) fut approuvé par la Conférence Interairline du B747, et fut utilisé pour développer le programme de maintenance du B747.
La méthodologie MSG évoluera en trois étapes suivantes :
• MSG‑2 (Airline-Manufacturer Maintenance Program Planning Document) publié le 25 mars 1970 par le sous-comité R & M de l’Air Transport Association américaine et qui fut utilisé pour le DC10 et le Lockheed 1011 ;
• EMSG (European Maintenance System Guide) préparé en 1972 et publié en février 1973 par l’Association of European Airlines. Il fut utilisé pour l’A300B2 et B4, le Concorde et le VFW614 ;
• enfin le MSG‑3 (Airline-Manufacturer Maintenance Program Development Document) publié le 30 septembre 1980 par une task force MSG‑3 de l’Air Transport Association américaine. Ce document fut amendé en 1988 (révision 1) et en 1993 (révision 2). Il sert pour tous les avions les plus récents : A310, A300-600, A319-320–321, A330-340, B757-767–777.
Le MSG‑3 est découpé en trois sections spécifiques :
• Programme moteurs et systèmes (SPP) établi avec les analyses MSI,
• Programme structure établi avec les analyses SSI,
• Programme d’inspection de zone (ZIP) établi avec les analyses zonales.
Pour développer le premier programme d’inspection et de maintenance d’un nouveau type d’avion, l’industrie met en œuvre la procédure du Maintenance Review Board décrite par la FAA dans une Advisory Circular (AC 121–22). Une organisation à trois étages est mise en place :
• un comité directeur (Industry Steering Committee), présidé par les compagnies aériennes,
• des groupes de travail communs constructeur-compagnies aériennes (Maintenance Working Group) présidés par le constructeur. Ils travaillent dans six domaines : mécanique-hydraulique, environnement et intérieur, moteur-carburant, électricité-avionique, structure, zonal inspection,
• et un Conseil supérieur (Maintenance Review Board) où ne siègent que les autorités de certifications et qui approuve les travaux réalisés qui seront publiés sous forme d’un Maintenance Review Board Report.
Les autorités de certification (JAA et FAA) participent également à l’ISC et aux Maintenance Working Groups.
Il est remarquable que ces travaux sont élaborés en commun entre les trois parties concernées par la sécurité : autorité, constructeur et exploitants.
Les groupes de travail utilisent les directives regroupées dans un Policy & Procedures Handbook (PPH) édité pour chaque type d’avion et regroupant les informations les plus récentes tant réglementaires que provenant de l’expérience en service.
Programme moteurs et systèmes
Les évaluations selon la méthodologie MSG‑3 sont fondées sur les défaillances fonctionnelles et les causes de ces défaillances.
Avant que le processus MSG‑3 puisse commencer il faut identifier les Maintenance Significant Items (MSI). Ceci est fait par une étude du Constructeur faisant appel au jugement technique de ses spécialistes. La sélection de MSI identifie les points qui :
• peuvent mettre en jeu la sécurité (au sol ou en vol), ou
• peuvent rester non détectés pendant l’exploitation, ou
• en dernier lieu, peuvent avoir un impact important sur la disponibilité opérationnelle ou l’économie de l’avion.
Cette première analyse donne la liste des MSI sélectionnés, matière première du processus MRB et de l’analyse MSI.
Le rapport d’analyse MSI comprend les informations liminaires classiques d’un document technique (liste des pages et numéro de date de publication, liste et raisons des révisions du document, applicabilité – modèles d’avions concernés par le document).
Sont également décrits les composants du système, leur fiabilité (MTBF et MTBUR), les redondances du système ainsi que l’expérience accumulée sur d’autres programmes similaires.
Vient ensuite la description de l’item lui-même : architecture du système, ses composants, les fonctions recherchées, les défaillances fonctionnelles, etc., qui doivent être analysées.
L’ensemble de ces données sont regroupées dans une DATA SHEET A.
L’analyse commence par identifier quatre points : les fonctions (points caractéristiques en fonctionnement normal), les défaillances fonctionnelles (quelles défaillances fonctionnelles peuvent se produire), les effets des défaillances (quel est le résultat de ces défaillances fonctionnelles), et enfin les causes (pourquoi la défaillance fonctionnelle s’est produite). Ces points sont détaillés dans une DATA SHEET B.
Chaque cause de défaillance est ensuite évaluée en suivant l’arbre d’analyse logique du MSG‑3.
Il comporte deux niveaux : d’abord l’examen de chaque défaillance fonctionnelle selon quatre questions pour déterminer la Failure Effect Category (FEC), puis la prise en compte des causes de la défaillance pour déterminer à travers cinq questions le type de tâche à appliquer.
La figure 2 montre l’arbre d’analyse logique et les cinq catégories dans lesquelles elles peuvent être classées : évidente critique, évidente opérationnelle, évidente économique, cachée critique, cachée non critique.
Le deuxième niveau d’analyse détermine quel type de tâche de maintenance doit être assigné à cet item en prenant en compte les causes de la défaillance.
Cinq types de tâches sont définis :
• lubrification-réfection des niveaux,
• vérification visuelle ou opérationnelle,
• inspection ou vérification fonctionnelle,
• remise en état,
• remplacement.
L’analyse permet de sélectionner la ou les tâches de maintenance ainsi que la périodicité d’application pour l’item considéré.
Les résultats de ces analyses sont regroupés dans des feuilles de synthèses qui doivent être validées par le comité directeur (ISC) avant de pouvoir être approuvées par le conseil supérieur (MRB).
Pour compléter leur travail, les groupes de travail doivent détailler chaque tâche suffisamment pour que les rédacteurs de la documentation d’entretien puissent la traduire en procédure d’entretien tout en respectant les intentions du groupe de travail.
Enfin, pour tirer bénéfice du programme d’inspection de zone (ZIP, voir plus bas), les tâches d’entretien qui préconisent une inspection visuelle générale peuvent être transférées vers le ZIP, dès lors que leur fréquence d’application est respectée. Ceci permet d’éviter des duplications inutiles.
![]() |
Les exigences découlant de la certification (CMR)
Les travaux de certification de type de l’avion identifient, entre autres, des tâches de maintenance. Par ailleurs les autorités de l’aviation civile introduisent des exigences spécifiques. Notamment, le constructeur doit faire une analyse de sécurité des systèmes (SSA) requise par le paragraphe JAR 25.1309.
Dans certains cas, pour obtenir le niveau de fiabilité nécessaire, des tâches de maintenance doivent être prescrites.
Ces travaux sont conduits par un comité spécifique : le Comité de coordination certification et maintenance qui examine les exigences découlant de la certification ou CMR (Certification Maintenance Requirements), qui retient la liste définitive et les classe en deux catégories :
• les CMR* (CMR one star) : tâches d’entretien dont les intervalles d’application ne pourront pas être modifiés par les opérateurs sans l’accord préalable du constructeur et de l’autorité de certification ;
• le CMR** (CMR two stars) : tâches d’entretien dont les opérateurs peuvent modifier la périodicité d’application selon les procédures d’évolution approuvées dans leur pays.
Les CMR sont publiés dans un document annexé en complément au rapport MRB.
Programme structure
La structure de l’avion est analysée pour déterminer les points nécessitant une surveillance ; on distingue deux grandes catégories :
Les items significatifs (SSI, Structural Significant Items) qui entreront dans le programme structure. Entrent dans cette catégorie les items qui contribuent significativement aux charges de vol, charges au sol, pressurisation et contrôle de trajectoire, et dont la défaillance menace l’intégrité de la structure et la sécurité de l’avion.
Et les autres points à surveiller qui seront pris en compte dans le programme de surveillance de zone.
La sélection des SSI dépend de deux facteurs :
• les conséquences de la défaillance (emplacements critiques) : on identifie les emplacements qui contribuent significativement à passer les charges et dont la tolérance au dommage ou la vie-sûre ont besoin d’être confirmées ;
• la probabilité de défaillance, déterminée selon la connaissance des applications de charge, de l’environnement et l’identification des emplacements qui, les premiers, développeront des dommages selon l’une des trois causes de dommage (dommage accidentel, détérioration due à l’environnement et dommage de fatigue).
Typiquement, les points exposés à ces dommages et qui entrent dans cette catégorie sont : les assemblages de sous-ensembles majeurs, les joints statiques nécessitant des graissages, les zones sensibles à la fatigue telles que points de concentration de charge, discontinuités, assemblages en tension ou alternant tension et compression, ferrures majeures, découpes dans panneaux, portes et hublots, etc. Sont concernées aussi les zones exposées à la corrosion (telles que toilettes, galleys, fonds de fuselage et zones de corrosion sous tension). Également prises en compte les zones vulnérables aux chocs extérieurs accidentels ou aux erreurs de maintenance (telles que seuils d’entrée, zones fréquemment concernées par des actions de maintenance ou exposées à des éclaboussures et fuites de liquides corrosifs). Enfin dernière catégorie, les items à vie-sûre.
L’analyse MSG‑3 appliquée à la structure
Comme pour les systèmes et moteurs, une méthodologie d’analyse logique est appliquée aux items SSI. Un arbre de décision logique a été adapté à l’analyse des SSI qui conduit à :
• distinguer les items tolérants au dommage et les items à vie-sûre,
• pour les items tolérants au dommage et les zones exposées aux dommages environnementaux ou accidentels, déterminer la faisabilité et le type de technique de surveillance.
L’analyse conduit à trois résultats possibles, soit le retour au bureau d’étude pour renforcer la résistance structurale, soit le classement dans l’une des deux listes du programme structure :
• liste des Airworthiness Limitations Items (ALI),
• programme consolidé d’entretien structural.
Chaque analyse est supportée par un dossier individuel (SSI Analysis).
L’approbation du programme proposé par le groupe de travail suit la même procédure que pour les systèmes et moteurs : présentation et critique par l’Industry Steering Committee, soumission au Maintenance Review Board aboutissant à l’approbation du programme structure intégré dans le MRB Report.
Analyse des dommages accidentels
Airbus a comme politique de ne pas créer de tâches d’entretien couvrant les dommages accidentels.
Les items sont donc analysés pour évaluer leur impact éventuel sur le comportement en fatigue ou la résistance à la corrosion. Si l’impact est significatif, il est pris en compte dans l’analyse SSI correspondante et se traduit, si nécessaire, par des tâches d’inspection structurale supplémentaires.
Analyse des dommages dus à l’environnement
Les structures métalliques sont exposées à de multiples variétés de corrosion : corrosion sous tension, galvanique, intergranulaire, filiforme, microbiologique, par frottement, piqûres ou même étendue.
Chaque item est évalué en fonction de son exposition, du type de corrosion susceptible de se développer et les résultats classés en fonction de leur sévérité afin de déterminer les intervalles d’inspection nécessaires.
Trois niveaux de sévérité sont internationalement reconnus :
• niveau 1 de corrosion : corrosion apparaissant entre deux inspections et qui peut être traitée dans les tolérances admises, ou corrosion dépassant les limites admises mais ne se produisant pas dans les conditions d’utilisation normales de l’avion,
• niveau 2 de corrosion : corrosion apparaissant entre deux inspections dont le traitement dépasse les limites admises et nécessitant une réparation ou un renfort structural,
• niveau 3 de corrosion : corrosion découverte lors d’une inspection, considérée comme menaçant la sécurité de la structure et nécessitant une réparation immédiate.
Les règles du MSG‑3 dans sa révision 2 de 1993 demandent qu’un programme de prévention et de contrôle de la corrosion (CPCP, Corrosion Prevention and Control Programme) soit établi par le constructeur pour permettre de contenir la corrosion au niveau 1.
Airbus a appliqué cette exigence non seulement pour ses nouveaux avions, mais aussi rétroactivement à toute sa gamme. Le CPCP est désormais incorporé comme partie intégrante du programme de maintenance structure.
Les composites nécessitent la prise en compte de facteurs spécifiques : d’autres sources de dégradation peuvent les endommager, telles que les actions de décapage ; par ailleurs, les chocs peuvent réduire brutalement la résistance d’un composite sans détection apparente.
Airbus prend en compte ces aspects au niveau de la conception : les défauts mettant en péril la résistance de la pièce en composites doivent être apparents de l’extérieur ; des tests sont réalisés pour démontrer que les dommages non visibles n’ont pas une importance critique pour la résistance de la structure.
Les » ALI » (Airworthiness Limitation Items)
Sont regroupés dans cette catégorie tous les items de fatigue critiques et ceux liés aux cycles de vol ainsi que les items critiques de corrosion.
Ces tâches liées à la fatigue et la tolérance au dommage sont très strictement encadrées. Les seuils de première inspection et les intervalles de répétition ne peuvent pas être modifiés par les opérateurs ou leur aviation civile sans l’accord du constructeur et de son autorité de certification.
Le document regroupant les ALI est un élément constitutif du programme d’entretien structure.
Les opérateurs doivent obligatoirement faire un compte rendu au constructeur pour toute découverte de dommage sur un item de la catégorie Airworthiness Limitation. Un formulaire est inclus dans le rapport MRB.
Programme d’inspection de zone (ZIP)
Principes généraux
Le programme d’inspection par zone (ZIP, Zonal Inspection Program) fournit les exigences d’inspection visuelle de l’ensemble de l’avion, par zones successives et couvrant les systèmes, les moteurs et la structure pour s’assurer de leur bon état général et maintenir la sécurité.
Chaque zone est clairement définie, avec des frontières facilement identifiables ; toutes les trappes d’accès sont ouvertes pour ces inspections.
L’avion est découpé en huit zones majeures :
• fuselage inférieur jusqu’à la cloison pressurisée arrière,
• fuselage supérieur jusqu’à la cloison pressurisée arrière,
• section arrière et empennage,
• moteurs, pylônes et nacelles,
• aile droite,
• aile gauche,
• train d’atterrissage et trappes de train,
• portes d’embarquement passagers et cargo.
Ces zones majeures sont divisées en zones plus petites pour faciliter la réalisation des travaux d’inspection. Des conventions de numérotation permettent un repérage logique entre zones symétriques ainsi qu’entre zones voisines.
La figure 3 donne un exemple des repérages pour les moteurs gauches d’un A340 (moteurs 1 et 2).
Il n’y a qu’un type de tâche dans le programme ZIP : inspection générale visuelle.
Chaque zone est analysée pour identifier les types de détériorations ou dommages susceptibles d’apparaître en service.
Toutefois, l’inventaire n’a pas la prétention d’être exhaustif ; on considère que le technicien réalisant l’inspection doit avoir une bonne connaissance de la construction de l’avion et des systèmes situés dans la zone qu’il inspecte. Les tâches d’inspection ZIP vérifient :
• les parties visibles de la structure et recherchent les dégradations telles que dommage accidentel, corrosion, frottements et interférences, fuites, fissures et état général des rivets et fixations,
• le bon état d’installation (et le freinage) des équipements, harnais, conduits, tubulures, poulies, etc.,
• l’état des capots, carénages, panneaux ouverts ou démontés pour accéder à la zone.
Les seuils de première inspection et les intervalles de répétition utilisent les mêmes unités de programmation que les autres opérations d’entretien : check A (500 heures) et multiples de A, check C (quinze mois) et multiples de C, cinq ans et dix ans.
Les seuils et intervalles les plus courts visent les points affectés par des dommages accidentels ou ayant des conséquences sur la fiabilité de l’avion ; ils nécessitent peu d’accès et à des zones bien spécifiques. Les seuils et intervalles plus longs exigent un niveau d’accès plus approfondi et visent des dommages qui se sont propagés pendant l’utilisation à un point tel qu’ils sont détectables par une inspection générale visuelle.
On a vu précédemment que des tâches peuvent être transférées des programmes d’entretien structure et moteurs systèmes. Dès lors que les tâches sélectionnées sont des inspections générales visuelles et que les fréquences de programmation sont cohérentes, elles sont reportées sur le programme ZIP. Ceci évite les duplications de tâches tout en répondant aux exigences de ces programmes d’entretien.
Analyse de tâche ZIP
Comme pour les autres volets du programme d’entretien, une méthode logique d’analyse est appliquée pour déterminer les intervalles des tâches ZIP.
Trois paramètres sont pris en compte :
• la densité : selon que les éléments installés dans la zone sont très rapprochés, l’inspectabilité de chacun d’entre eux et de la structure en est affectée ;
. l’importance : l’importance de chaque composant en termes de sécurité ou de coût de fonctionnement est évaluée. On prend également en compte les dommages qu’une défaillance peut provoquer sur les éléments adjacents de la zone ;
. l’environnement : on évalue l’exposition à la chaleur, aux vibrations ou aux dommages accidentels.
Ces trois paramètres sont ensuite combinés selon une logique de décision pour déterminer l’intervalle souhaitable d’inspection.
Ces évaluations font appel au jugement personnel des spécialistes, au retour d’expérience sur les flottes en service avant d’arrêter la décision découlant de l’analyse logique. C’est ainsi qu’on peut aboutir à un programme d’inspection qui soit à la fois praticable et réaliste.
Le rapport MRB
Ce rapport fournit aux opérateurs le programme minimum et initial de l’avion, avec les tâches et leur fréquence d’application pour les moteurs, les systèmes et la structure. L’objectif de ce document est de servir de base à l’élaboration par chaque opérateur de son propre programme de maintenance qui sera approuvé par les autorités de son pays.
L’organisation du rapport reflète l’organisation des travaux dont il regroupe les résultats :
• Introduction,
• Règlements généraux applicables à tout programme d’avion,
• Programme systèmes et moteurs,
• Programme structures,
• Programme d’inspection de zone,
• et un chapitre spécifique : Exigences spécifiques américaines.
S’y ajoutent les deux annexes :
• CMR (exigences découlant de la certification) et Limitations de navigabilité (ALI),
• Diagramme de zone, Glossaire, Abréviations, etc.
LE MPD (Maintenance planning document)
Comme indiqué ci-dessus, le rapport MRB ne donne que le programme initial d’entretien de l’avion, au moment de la première mise en exploitation commerciale. Le MPD est destiné à prendre la suite de ce document initial pour incorporer les évolutions durant la vie de l’avion qui peut durer trente ans ou plus.
Ces évolutions sont tirées de cinq sources différentes : les consignes de navigabilités imposées par les autorités de certification, les SIL (Service Information Letters) du constructeur, les services bulletins pour inspection, les services bulletins pour modification et les évolutions de vie-sûre. Leurs impacts sur les tâches de maintenance et leur périodicité sont incorporés en permanence dans le MPD.
Conclusion
De la description de ces processus d’élaboration des programmes d’entretiens d’avions, on retiendra plusieurs points fondamentaux.
La méthodologie moderne a trouvé ses fondements à la fin des années soixante, succédant à quarante ans d’empirisme et de tradition ; elle a ensuite progressé au cours des années 1970 à 2000 parallèlement aux progrès techniques des avions et en perfectionnant les méthodes précédemment utilisées.
Les principes mis en œuvre font appel à une logique relativement simple, qui trouve sa puissance dans la rigueur de son application et le détail des analyses.
Il est fait appel constamment à l’expérience acquise, la compétence et la connaissance détaillée de l’avion détenues par tous les acteurs : non seulement les ingénieurs concepteurs (le bureau d’étude), mais aussi les techniciens de l’après-vente du constructeur, des spécialistes de compagnies aériennes, et ceux des aviations civiles.
La collaboration entre ces trois parties (constructeur, compagnies et aviation civile) se fait à la fois dans l’interactivité (groupe multiparties) et dans l’alternance des pouvoirs (approbations en deux étapes, par les compagnies puis par les aviations civiles).
Enfin, la responsabilité ultime revient à la compagnie aérienne. Conformément au droit aérien international, chaque pays étant souverain, le constructeur fournit les données nécessaires aux exploitants mais n’exerce pas une tutelle sur eux.
Il reste que la complexité et la longue accumulation d’expériences nécessaires pour élaborer ces programmes de maintenance font que peu d’aviations civiles et peu de compagnies se sentent qualifiées pour décider d’elles-mêmes d’écarts importants par rapport aux recommandations du constructeur.
Ainsi, une certaine cohérence mondiale est réalisée : les principes généraux utilisés en début de processus sont uniformes et suivent les recommandations de l’OACI. Et en bout de processus, les programmes individuellement appliqués par les exploitants sont très proches les uns des autres, tant il est complexe de s’écarter du programme recommandé par le constructeur.