Le futur de la propulsion d’hélicoptère
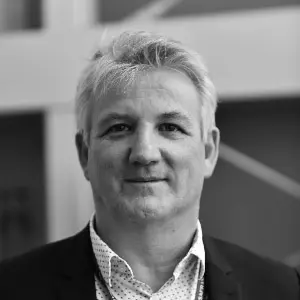
Le mode de propulsion des hélicoptères est bien sûr un des lieux principaux d’innovation pour développer l’hélicoptère du futur. Où en est-on ?
Le développement des turbomoteurs jusqu’alors obtenu par des améliorations incrémentales doit, pour la prochaine génération, venir de technologies en rupture. C’est un changement complet de paradigme et de nombreux défis sont à relever, toutes les phases de vie du turbomoteur sont concernées, depuis sa conception, sa fabrication, jusqu’à sa maintenance. De nouveaux moyens de conformité à la réglementation restent à imaginer.
REPÈRES
La recherche et développement au sein de Safran vise à garantir, dans la durée, l’excellence technique et la différenciation technologique de l’entreprise pour répondre aux défis de l’avenir. Elle est à la fois décentralisée au sein des sociétés du groupe et complétée, pour les activités transverses et amont, par un pôle central de recherche et d’innovation. Les dépenses R & D représentent 8 % du CA soit 1,7 milliard d’euros en 2020 et mobilisent 16 % des effectifs du groupe, dont environ un millier d’ingénieurs chez Safran Helicopter Engines. Safran se place depuis plus de huit ans dans le trio de tête des entreprises françaises ayant publié le plus de demandes de brevet, avec plus de 1 000 pour l’année 2020. C’est toujours à Bordes que sont conçus les moteurs et qu’ils y sont en grande partie fabriqués. De même se perpétue la tradition de baptiser les moteurs avec des noms d’inspiration pyrénéenne.
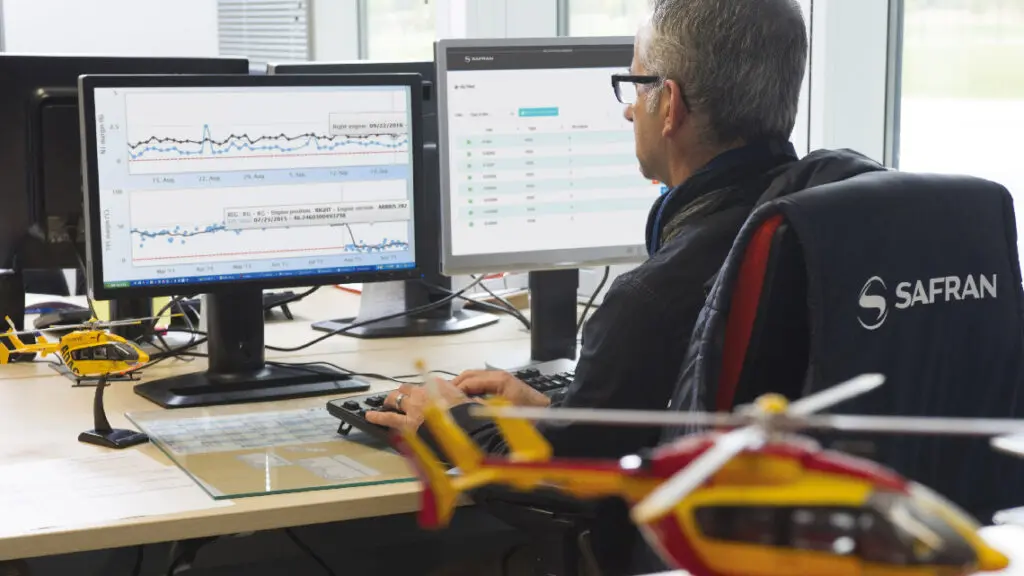
Les spécificités du turbomoteur
L’hélicoptère couvre un large spectre de missions nécessitant une grande plage de puissance. Le turbomoteur est dimensionné par la puissance nécessaire au décollage, entraînant des compromis sur le rendement pour les puissances intermédiaires. Ce rendement, exprimé par la consommation spécifique, varie de façon décroissante de la puissance. La densité de puissance est un autre paramètre fondamental sur les appareils à décollage vertical.
La recherche de compacité des turbomoteurs, pour des puissances relativement faibles entre 400 et 2 000 kW, présente des difficultés de fabricabilité de par la taille réduite des composants, pénalisant aussi le rendement global et la tenue thermomécanique. Le système carburant et son calculateur numérique jouent un rôle essentiel par l’adaptation de la puissance aux besoins du rotor. Il contribue à la sécurité et à la manœuvrabilité de l’hélicoptère en garantissant sa portance.
Les turbomoteurs du futur
La sécurité est la priorité absolue ; l’amélioration continue de la fiabilité des turbomoteurs permet d’afficher des taux meilleurs qu’une panne par 100 000 heures de vol. Mais la quête de toujours plus de sécurité se poursuit, avec les objectifs fixés par les organismes de sécurité aérienne dont l’idée est de réduire le taux d’accident de 80 %. Même si l’hélicoptère réalise beaucoup de missions d’utilité publique, le bruit est un facteur de nuisance. Le turbomoteur est une des sources d’émissions acoustiques qui peut devenir prépondérante comparativement au bruit rotor. Le coût d’utilisation du moteur est aussi un facteur clé de succès, il représente plus de la moitié du coût d’utilisation pour un hélicoptère léger.
L’attente des clients est une maintenance individualisée et une disponibilité accrue. Aujourd’hui la transition écologique est aussi une priorité. Si aucune législation n’existe à ce jour, l’Organisation de l’aviation civile internationale pourrait imposer des exigences pour les futures conceptions. Les émissions de CO2, directement liées à la consommation, sont proportionnellement faibles par rapport aux autres applications aéronautiques. L’usage en zone urbaine requiert également de réduire les autres polluants, comme l’oxyde d’azote ou les particules fines.
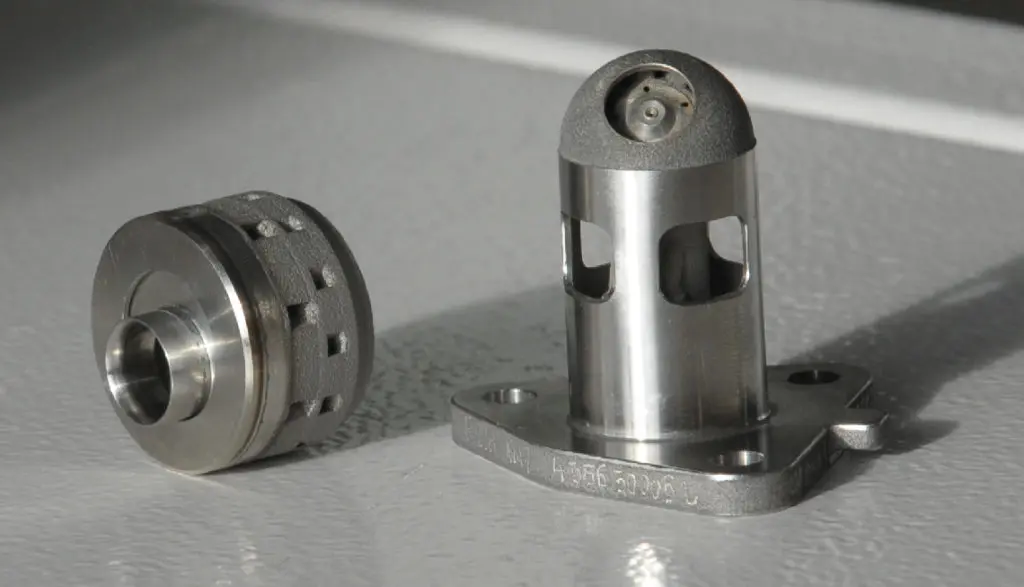
des fonctions entraînant des formes complexes non réalisables par des procédés conventionnels.
Les réponses technologiques
Les réponses technologiques s’articulent autour de quatre grands axes : des turbomoteurs toujours plus efficaces et compacts ; l’usage de carburants durables à la place du kérosène ; l’hybridation électrique en assistance ou complément de la turbine ; le traitement des données de vol.
Le turbomoteur à haute efficacité
En 50 ans, la densité de puissance a été augmentée de 160 % et le rendement de 45 %. Ces gains sont liés aux évolutions des taux de compression et à une meilleure tenue en température des pales de turbine. Les objectifs de la prochaine génération sont de gagner 20 % supplémentaires sur le rendement et donc autant sur les émissions de CO2, ainsi que 10 % sur la densité de puissance. L’amélioration des compresseurs passe par la contrainte sur le rapport de pression qui ne peut pas dépasser certaines valeurs, afin de limiter la taille des compresseurs. Le rendement des turbines est directement lié à leur fabricabilité. Pour dépasser ces limites, les géométries 3D en modélisation, conception et fabrication doivent être parfaitement maîtrisées. Des nouveaux matériaux monocristallins permettent de repousser toujours plus loin les limites de température.
Les travaux sur les émissions conduisent aussi à travailler sur des combustions à circuit d’injection étagé ou à richesse contrôlée, permettant de limiter les montées en température – sources d’oxyde d’azote. Pour l’acoustique, les travaux portent sur la réduction des bruits des deux sources, la combustion et la compression de l’air. La modélisation des phénomènes et leur prise en compte dans la conception des composants sont un élément clé pour intégrer des dispositifs d’atténuation. La fabrication additive permet de mutualiser des fonctions entraînant des formes complexes non réalisables par des procédés conventionnels.
Par exemple, la pulvérisation des injecteurs de carburant est améliorée en les entourant d’un flux d’air dont la dynamique est optimisée par des éjecteurs que seule la fabrication additive rend possible. Des gains en masse sont aussi envisageables. Les principaux défis à relever sont la répétitivité du procédé, la constance des propriétés des matériaux et la démonstration garantissant une non-régression de la sécurité dans le temps.
Les carburants alternatifs durables
Les biocarburants sont aujourd’hui autorisés jusqu’à un mélange à 50 % avec le kérosène, l’extension à un usage à 100 % est à l’étude. Ces carburants issus de la biomasse, dont les filières restent à développer, ont des propriétés physicochimiques proches du kérosène mais pas complètement identiques. Ils sont plus pauvres en aromatique et en soufre, deux composés assurant le pouvoir lubrifiant, et donc peuvent potentiellement entraîner une usure prématurée des pièces ou amoindrir la tenue mécanique des élastomères des joints. Certains carburants alternatifs sont issus de matières premières hydrophiles qui peuvent capter l’humidité ambiante et engendrer des problèmes de fonctionnement. Pour des aspects logistiques, les nouvelles chambres de combustion devront aussi autoriser le fonctionnement du turbomoteur indifféremment de la nature du carburant, qu’il soit d’origine fossile, biomasse ou de synthèse.
“La sécurité est la priorité absolue.”
L’hybridation électrique propulsive
La faible densité en puissance et énergie des batteries ne permet pas à des systèmes tout électrique de rivaliser avec une turbine, même en tenant compte des projections à long terme de performance des batteries. C’est pourquoi les applications envisagées pour l’hybridation électrique dans la prochaine génération de turbines sont des apports ponctuels de puissance en assistance ou en complément du turbomoteur.
Les gains attendus sont de deux ordres : une baisse de la consommation carburant en faisant fonctionner la turbine avec un meilleur rendement ; mais aussi des effets au niveau de l’aéronef. Sur les hélicoptères de type monomoteur, la source électrique peut apporter transitoirement de la puissance au rotor via une machine électrique. La sécurité est ainsi améliorée, car la source électrique autorise un vol de quelques minutes en cas de panne de la turbine. Le pilote peut se poser dans une zone dégagée plutôt que de faire une manœuvre d’autorotation (atterrissage moteur éteint) délicate à gérer.
Les principaux défis de l’hybridation électrique sont la densité des composants électriques et des organes de stockage, la sécurité pour protéger les passagers et les systèmes des effets de la haute tension (plusieurs centaines de volts) qui alimente les machines électriques. De nouveaux modes de défaillance comme les décharges partielles ou les arcs électriques nécessitent de développer des protections électrotechniques spécifiques.
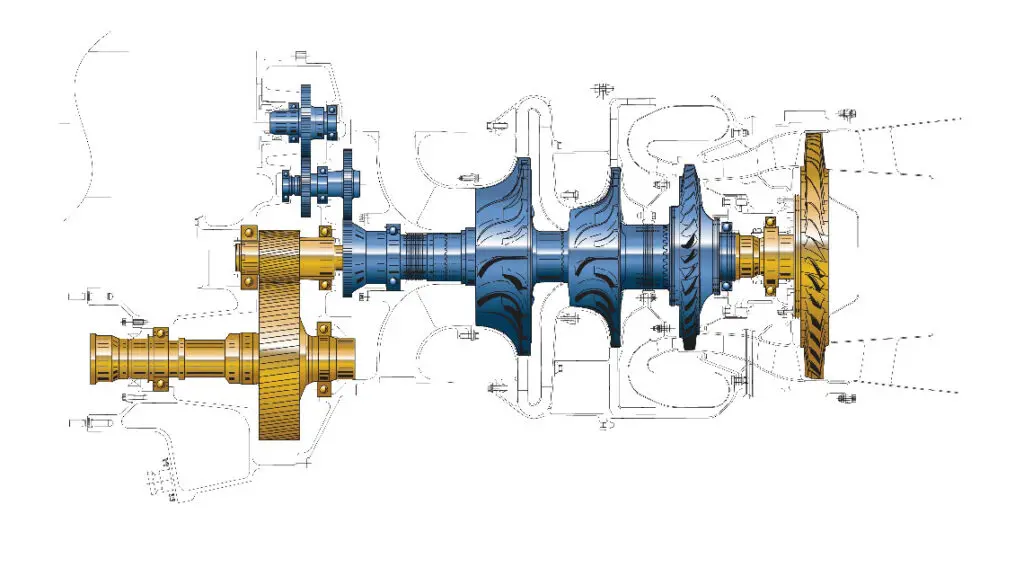
1. Boîtier réducteur
2. Compresseur à deux étages centrifuges
3. Chambre à combustion giratoire
4. Turbine haute pression
5. Turbine libre
La digitalisation au service des clients
Les opérations de maintenance sont aujourd’hui périodiques et les mêmes quelles que soient les missions. Demain, il sera possible de proposer une maintenance personnalisée et de réduire le temps d’immobilisation de l’hélicoptère. La collecte et l’analyse de la donnée sont au centre de nouveaux concepts. Une maintenance selon « état » fondée sur la surveillance d’indicateurs de santé et la prédiction de défaut via la modélisation embarquée d’un jumeau numérique du turbomoteur. Une maintenance selon « usage », basée sur l’analyse des missions avec une cartographie d’entretien adaptée.
Les technologies à développer sont multiples, depuis des calculateurs à grande capacité de stockage, des capteurs intelligents, de la connectivité avec la contrainte grandissante de la cybersécurité, l’analyse de données complétée par l’utilisation de l’intelligence artificielle. Un des défis est de convaincre les autorités de certification de la fiabilité des traitements algorithmiques des données pour ne pas remettre en cause l’accidentologie.