Roxel : Un leader européen de la propulsion

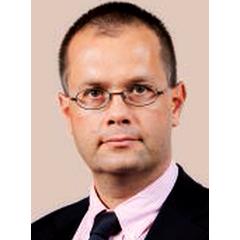
Quelques mots pour nous Roxel ?
Jacques Desclaux : Roxel est le leader européen de la propulsion tactique et le numéro 3 mondial derrière les États-Unis. Roxel conçoit, développe, industrialise, produit et commercialise tous les types de moteurs solides pour systèmes d’armes tactiques, missiles de croisière et d’autres applications comme les cibles aériennes, par exemple.
Nous exportons une partie de nos produits en direct soit 1⁄3 de notre chiffre d’affaires. Le reste de notre chiffre d’affaires est réalisé auprès de MBDA, le leader européen au niveau des systèmes d’armes, qui est notre principal client.
Notre cœur de métier est la conception même du moteur en combinant les connaissances chimiques, mécaniques et thermiques de manière à garantir le fonctionnement requis par les spécifications précisées par nos clients.
Que représente le marché de la propulsion et quel est votre positionnement ?
J.D : La richesse des programmes américains sur les segments de systèmes d’armes au sol, de plateformes aéroportées et maritimes explique le leadership des États-Unis sur ce marché.
Roxel couvre également tous ces segments et dispose de toutes les technologies nécessaires pour exercer efficacement ce métier. Nous capitalisons sur nos expertise et expérience pour participer et contribuer à des projets emblématiques dans le cadre desquels nous prenons en charge les aspects ayant trait à la propulsion.
Les 25 dernières années ont connu une décroissance continue de l’activité, qui est, entre autres, liée à la baisse des budgets alloués à la défense aussi bien en France qu’en Europe.
En 2014, nous avons réussi à stopper cette tendance. Depuis 2015, nous sommes repartis sur une phase de croissance et nous espérons augmenter notre activité et notre chiffre d’affaires de 30 % d’activité sur les 5 prochaines années.
Afin de soutenir notre développement, nous misons sur l’innovation et l’investissement. Nous avons investi plus de 20 millions d’euros pour une nouvelle usine dédiée au propergol composite qui est un mélange très énergétique utilisé pour la propulsion solide.
Cette capacité à faire travailler des chimistes et des mécaniciens ensemble reste une de nos plus grandes force et richesse. Il est important que ces deux métiers collaborent et allient leurs compétences afin de s’auto-fertiliser.
Quelle est votre approche de l’innovation ?
Dispositif durant malaxage – CARLA Technologie de rupture : le malaxage par résonance acoustique des propergols – il permet non seulement d’améliorer la qualité des produits, mais surtout il réduit les cycles de mise en œuvre par un facteur habituellement supérieur à 10 voire 100. Il donne accès au concept de « mix in place » qui permet de fabriquer à la demande et sans aucun rejet ou déchet des moteurs de missile tactique. © Roxel
Emmanuel Durliat : L’innovation est la clé du maintien de notre avantage concurrentiel. Elle nous permet de nous distinguer de la concurrence sur le plan de la performance et du coût de nos produits.
Nous travaillons sur l’optimisation de la performance industrielle à travers l’amélioration de nos procédés de fabrication. Nous visons la réduction des coûts ainsi qu’une meilleure agilité, réactivité et flexibilité pour répondre efficacement aux besoins de nos clients.
Nous avons aussi une activité dans l’aéronautique et nous participons par exemple au programme CORAC soutenu par Airbus. Nous développons un ensemble d’une nouvelle famille de matériaux qui permettra d’alléger de façon significative une partie du mat auquel le moteur est accroché à l’aile de l’avion. Nous apportons à Airbus une solution unique en termes de masse et de coût.
Sur le plan du développement durable, nous travaillons sur la réduction de notre empreinte environnementale en réduisant nos rejets par des procédés innovants et en remplaçant les produits impactés par les réglementations futures.
Comment vous démarquez-vous à ce niveau ?
E.D : Ce travail d’innovation est réalisé avec divers partenaires : des industriels, des PME innovantes ou des laboratoires universitaires comme le CNRS.
Cela nous permet de brasser les cultures et les expériences, de découvrir ce qui se fait dans les domaines connexes aux nôtres.
Nous misons également sur les technologies de rupture issues d’autres domaines. Ainsi, nous nous sommes appropriés une technologie issue de l’industrie pharmaceutique, le malaxage par résonance acoustique qui permet de réduire les déchets, d’avoir des matériaux de meilleure qualité et d’optimiser nos coûts et cycles industriels.
Nous sommes membres fondateurs d’une plateforme collaborative de fabrication additive qui s’organise autour du centre de recherche CETIM et qui est co-financée par les industriels.
Grâce à ces travaux de recherche, nous avons la capacité de fabriquer, en interne, des pièces allégées ou fonctionnalisées inaccessibles avec les procédés d’usinage standards.
C’est également une piste de réduction des coûts et des cycles surtout pour le prototypage rapide.
Quels sont les enjeux auxquels vous êtes confrontés et les axes de développement qui en découlent ?
J.D : Nos clients sont en perpétuelle demande de produits plus performants, à un coût compétitif et avec des cycles de développement et de livraison plus courts.
Fabrication additive de sous-ensembles de moteur de missile tactique : réduction de la masse de plus de 30 %, réduction des coûts, accès à des géométries non fabricables par les procédés conventionnels. © Roxel
Pour maîtriser les coûts, nous intervenons de plus en plus en amont dans la conception des produits.
Sur la réduction des délais, nous avons entrepris une démarche de simplification de nos processus.
Dans cette optique, nous utilisons les méthodes DMAIC, QRQC, Kaizen ou bien encore le management visuel pour traiter avec réactivité les problèmes ponctuels en impliquant toutes les parties prenantes.
Dans le cadre de nos investissements, nous essayons d’avoir un cheminement des pièces le plus « lean » possible.
Au niveau de la gestion des risques, nous avons créé des bases de données pour surveiller en continu nos procédés afin d’en augmenter la qualité et la fiabilité. Nous en sommes encore au stade d’atelier pilote et les premiers résultats sont très concluants.
La gestion des risques est de plus en plus intégrée dans nos procédés et processus afin de réduire l’occurrence ou la gravité des incidents. Nous sommes en train de passer la certification Qualité EN9100 pour l’ensemble de nos activités.
Et pour conclure, un mot pour notre lectorat ?
EN BREF
Roxel est une entreprise de taille intermédiaire spécialisée dans le domaine de la propulsion.
L’entreprise regroupe 575 collaborateurs et génère un CA de 120 millions d’euros.
Le groupe est organisé autour de deux filiales : Roxel France et Roxel UK.
J.D : Pour réussir et se démarquer, il faut se passionner pour les challenges et miser sur l’innovation et l’investissement. Contrairement à un grand groupe, au sein d’une PME, l’agilité et la polyvalence sont primordiales.
Les PME ont, en effet, besoin de profils dotés d’une grande autonomie et capables d’être suffisamment spécialistes sur une palette élargie de compétences. E.D : Il ne faut pas hésiter à commencer sa carrière dans les métiers techniques.
Une expérience technique permet de bien se préparer à des fonctions de management.