La sécurité industrielle : prévention des risques majeurs et sécurité au poste de travail
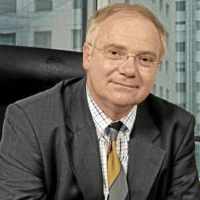
L’explosion du hangar 221 sur le site Grande Paroisse de Toulouse a causé la perte de trente vies humaines et fait des centaines de victimes. Après l’immense émotion que cette catastrophe industrielle a provoquée – et continue de provoquer – dans tout le pays, et au-delà de la douleur que tous les salariés d’Atofina ressentent à l’égard de leurs amis ou collègues et leurs proches, vient, pour l’entreprise, l’heure de sortir de sa réserve.
Ce drame aujourd’hui encore inexpliqué et le deuil que nous portons constituent pour l’ensemble du groupe TotalFinaElf et pour sa branche chimie un ardent appel à réaffirmer nos priorités en matière de prévention des risques et d’ouverture vis-à-vis des populations qui vivent à proximité de nos installations.
La prévention des risques majeurs
La prévention des risques majeurs débute aux phases de recherche et de conception. Atofina fabrique ainsi plusieurs milliers de produits et s’est doté, depuis de nombreuses années, de moyens d’essais et de calculs des risques industriels permettant d’évaluer les dangers des nouveaux produits, des procédés et des schémas de fabrication envisagés. Le principe de réduction du risque à la source est appliqué à toutes les étapes de développement jusqu’à la construction et à l’exploitation des procédés mis en œuvre.
De même, on évalue certains scénarios d’accident industriel de référence, de probabilité très faible, mais qui permettent de dimensionner les moyens de protection (par exemple le degré de résistance des salles de contrôle) ou d’intervention (incendie, secours) et d’estimer également l’impact d’événements de type accidentel à l’extérieur du site (zones de danger).
C’est l’ensemble de ce processus, véritable » clef de voûte » de la réglementation en matière d’installations classées, qui est formalisé dans les » études de danger « , à caractère obligatoire pour les unités industrielles présentant un certain niveau de risque.
En matière de prévention des risques majeurs, on identifie cinq axes de vigilance :
- la sécurité des procédés, qui constitue le cœur de notre métier de chimiste (voir encadré),
- la maîtrise des opérations de stockage, de conditionnement et de manutention des produits et des matières premières : dans ce domaine s’impose une réflexion globale pour privilégier des solutions qui minimisent le risque lié au transport des matières dangereuses,
- la sûreté de nos installations, c’est-à-dire leur protection vis-à-vis d’agressions ou d’actes de malveillance pouvant venir de l’extérieur de l’entreprise,
- l’implantation et la protection de nos installations avec, en particulier, le renforcement des salles de contrôle contre une sollicitation résultant de situations accidentelles,
- la maîtrise de l’urbanisme autour de nos sites, thème sur lequel une réflexion nationale a été engagée mais pour lequel l’industriel peut, d’ores et déjà, apporter sa contribution en améliorant la communication avec les collectivités locales.
Ces cinq axes de travail mobiliseront, dans les années à venir, des investissements importants.
La sécurité au poste de travail
La sécurité au poste de travail concerne toutes les opérations liées à la conduite et à l’entretien de nos unités, et englobe un aspect essentiel en chimie compte tenu des dangers de toxicité que présentent certains des produits fabriqués : l’hygiène industrielle.
En matière de sécurité au poste de travail, deux axes majeurs de progrès permanent s’imposent :
- la réduction de la fréquence des accidents de travail, qui met en jeu des aspects techniques, organisationnels mais aussi culturels et de comportement individuel (voir schéma),
- l’amélioration constante de notre connaissance sur les caractéristiques toxiques des produits : à cet égard, l’entreprise collabore résolument au programme européen du CEFIC (Comité européen des fédérations de l’industrie chimique) et soutient dans son principe le projet du Livre blanc de la Commission européenne sur les produits et les substances dangereuses.
Autant il est aisé de mesurer l’évolution des progrès en matière de sécurité au poste de travail, autant il est complexe de quantifier le niveau d’efficacité en matière de prévention des risques majeurs, puisqu’il s’agit d’événements redoutés que l’on cherche à éviter. Dans ce domaine certains de nos voisins européens ont su développer des approches quantitatives du risque (QRA ou Quantified Risks Analysis) très prometteuses pour l’amélioration de l’appréciation et de la gestion de risque (voir encadré).
*
* *
À court et moyen termes, la Direction sécurité industrielle privilégie des actions situées dans les trois registres de l’organisation, de l’expertise et de la communication.
L’organisation du management de la sécurité
Des prescriptions générales pour l’ensemble de la branche chimie sont transposées sur chaque site industriel et adaptées à chaque situation locale. Dans l’industrie en général, plus des deux tiers des incidents sont dus au non-respect ou à la non-compréhension de ces règles. Il nous faut donc renforcer en permanence nos systèmes de gestion de la sécurité afin de ne pas oublier la dimension humaine ; pour cela, trois leviers sont disponibles :
- la formation de nos personnels et de ceux des entreprises qui interviennent sur nos installations,
- l’intensification des audits internes et externes,. et, pour les sites dont les niveaux de risques le justifient, la vérification par des experts extérieurs à l’entreprise de la bonne application de nos procédures :
- ainsi sera progressivement mis en place un système international d’évaluation de la sécurité.
L’expertise
Si l’Ineris (Institut national pour la protection de l’Environnement et des risques industriels) et l’IRSN (Institut de radioprotection et de sûreté nucléaire) sont les deux pôles publics indispensables d’expertise, il est essentiel qu’émergent de France d’autres centres de compétences, comme cela existe chez certains de nos voisins européens. À cet égard, le tissu des universités et des écoles de chimie reste encore trop peu exploité. Le Groupe TotalFinaElf a donc décidé de parrainer la naissance d’un Institut européen de la Sécurité industrielle, basé à Toulouse, qui s’appuiera sur les centres locaux de compétences, d’enseignement et de recherche.
En parallèle, on évalue et compare les différents modèles de quantification des risques en usage dans d’autres pays d’Europe (approche dite » probabiliste ») pour promouvoir dans les prochains mois, auprès de l’Union des industries chimiques et des autorités administratives, une approche permettant de faire évoluer les modalités d’appréciation du risque dans le contexte de la cohabitation entre les villes et les usines.
Communication
Depuis toujours, l’univers de la chimie souffre d’un déficit d’information. À l’image de ce qui a été accompli dans le secteur nucléaire, des progrès sont à réaliser pour expliquer les spécificités et la finalité de ses multiples métiers. Si la sécurité des installations et des personnes a toujours figuré au centre de ses préoccupations, la chimie a souvent fait preuve d’une trop grande discrétion dans ce domaine.
Nous devons nous ouvrir :
a) vers les partenaires sociaux de l’entreprise : à cet égard, les CHSCT sont des interlocuteurs privilégiés dont il convient d’améliorer l’efficacité par des actions de formation tenant compte de l’évolution des méthodes et des exigences ;
b) vers les collectivités locales : il a été décidé de promouvoir, dès aujourd’hui, au sein de l’Union des industries chimiques l’élaboration d’une échelle simplifiée de gravité des incidents, afin d’amorcer avec la communauté un dialogue dépourvu de tabou ;
c) vers nos riverains, qui sont aussi, souvent, des membres de notre personnel : la Société va, dans les mois qui viennent, renforcer ses contacts avec ses voisins et les communautés locales, pour les informer davantage de la matérialité des risques et de la finalité de notre mission d’industriel.
Au travers d’événements douloureux et de remises en cause brutales, l’industrie chimique doit aujourd’hui accepter que l’exercice de ses métiers ne puisse être durablement envisagé qu’à deux conditions :
- la finalité de ses activités doit être jugée légitime,
- l’exercice de ses activités doit être jugé tolérable.
C’est le sens de la mission confiée aux deux Directions du développement durable et de la sécurité industrielle au sein de l’entreprise.
Commentaire
Ajouter un commentaire
Je trouve très important les informations que vous nous donnez sur le management.