La révolution de la fabrication additive métallique

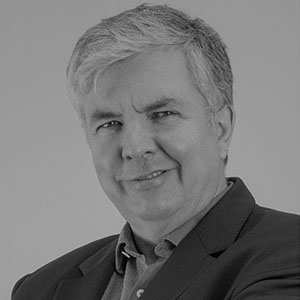
L’impression 3D de pièces en métal poursuit sa progression au sein de l’industrie mondiale. Les entreprises utilisant pleinement le potentiel d’innovation associé à cette technologie élaborent les premiers business cases attractifs, particulièrement aux États-Unis ou en Allemagne. La France dispose également d’une compétence reconnue en la matière et doit maintenant réussir son développement industriel.
Quel que soit le secteur industriel, il existe des applications potentielles pour la fabrication additive métallique. Le principe de cette technologie, par opposition à la fabrication soustractive, est de déposer du métal par couches successives en le fusionnant uniquement là où c’est nécessaire. La majorité des technologies métalliques utilisent de la poudre métallique seule, qui est fondue par une source d’énergie, mais certains procédés utilisent des mélanges de poudre et de liant, ce dernier étant éliminé au cours de la fabrication. La technologie la plus répandue est appelée fusion laser sur lit de poudre (LBM, pour Laser Beam Melting). C’est aussi la technologie la plus ancienne (une vingtaine d’années) et donc la plus mature. Elle consiste à déposer sur un plateau des couches de poudre métallique, dont une partie sera fusionnée par un faisceau laser.
Une autre technologie répandue est le dépôt sous énergie dirigée (DED, Direct Energy Deposition), qui consiste à projeter de la poudre dans un faisceau laser puis à déposer le métal en fusion pour fabriquer la pièce. Ce procédé permet de construire des pièces de grandes dimensions et de réparer des pièces existantes. Même si LBM et DED représentent 85 % des applications, il existe aujourd’hui de nombreuses technologies de fabrication additive métallique, et les industriels devront trouver le meilleur compromis pour leur application en considérant : la taille des pièces produites (de quelques microns à plusieurs mètres), la productivité et les coûts (de quelques cm3/h à plusieurs dm3/h ou de quelques dizaines d’€/kg à plusieurs centaines d’€/kg), le niveau de finition (niveau de détails de quelques microns à quelques millimètres), la finesse de l’état de surface et la qualité métallurgique et les propriétés mécaniques de la pièce finie.
REPÈRES
Venue du monde du polymère, la vague de l’impression 3D gagne désormais l’industrie. En particulier grâce aux technologies de fabrication additive métallique, comme en témoignent les nombreuses créations de start-up, l’émergence des premières licornes, la multiplication des levées de fonds et l’accroissement des investissements en R & D. Les projections de marché (ventes de machines, matériaux, impression et services associés) sont de l’ordre de 17 milliards d’euros pour 2020 et 35 milliards en 2024, avec une croissance annuelle de l’ordre de 20 % par an. Ainsi, en 2019 plus de 2 000 systèmes d’impression 3D métallique ont été vendus.
Des domaines applicatifs toujours plus larges
Le succès de l’impression 3D, ou fabrication additive, provient de la variété des applications potentielles, avec des bénéfices variés pour la plupart des secteurs industriels. La fabrication additive métallique est un déclencheur d’innovation et de performance. Elle offre une liberté inédite de conception et permet de réaliser des pièces complexes, impossibles à réaliser avec les techniques conventionnelles. Les principaux bénéfices de cette technologie sont présentés ci-après.
Premièrement, la fabrication additive permet de réaliser des pièces sans recourir à des outillages, et ainsi de produire rapidement des pièces uniques ou des petites séries. C’est la raison pour laquelle elle s’est d’abord diffusée dans le monde du prototypage. D’autres secteurs s’y sont rapidement intéressés, comme le sport automobile : en produisant de nombreuses variantes de pièces durant les phases d’essais entre les courses, la technologie permet d’adapter et d’améliorer les véhicules beaucoup plus rapidement. De même, le marché de la pièce de rechange automobile, même s’il est encore embryonnaire, présente des perspectives intéressantes.
Deuxièmement, la fabrication additive offre la possibilité de produire de grandes séries de pièces toutes différentes. On parle de personnalisation de masse, une capacité déjà exploitée par les industriels du dentaire et du médical. En scannant le patient et en imprimant une prothèse aux dimensions exactes de l’os à remplacer, ils réduisent les temps d’intervention et les temps de rééducation, ainsi que les coûts associés.
Troisièmement, le principe de fabrication par couches successives permet de réaliser des pièces moins massives que les procédés conventionnels, tels l’usinage ou l’injection. Les industriels de l’aéronautique et du spatial utilisent cette technologie pour produire des pièces toujours plus légères. Ils reconçoivent des équipements en se focalisant uniquement sur les parties fonctionnelles et atteignent des gains de masse supérieurs à 50 %.
Le dernier bénéfice de la fabrication additive, qui est aussi le plus important, est qu’elle donne l’occasion de repenser complètement certaines pièces ou systèmes, avec la possibilité de réunir plusieurs fonctions dans une même pièce. Il n’est pas rare qu’un assemblage de plusieurs dizaines de pièces puisse être regroupé en une seule. Outre les gains de masse, cette diminution du nombre de pièces génère des gains tout au long de la vie des produits, de la fabrication jusqu’à la maintenance. Surtout, la capacité à fabriquer des pièces complexes est l’occasion pour les industriels d’améliorer les performances de leurs équipements. Les pièces assurant de la circulation de fluides ou des échanges thermiques, tels les blocs hydrauliques ou les radiateurs ou des outillages (conformal cooling), peuvent voir leur efficacité nettement améliorée grâce à cette technologie.
“La fabrication additive
donne une liberté quasi totale de conception.”
L’exemple de Michelin
Dès le début des années 2000, Michelin a pressenti tout le potentiel de la fabrication additive pour les moules de cuisson de ses pneumatiques. Un moule, c’est un assemblage complexe de pièces, qui peut comporter jusqu’à plusieurs milliers de lamelles en acier (les lamelles étant les pièces qui créent les rainures dans les pneumatiques). Afin de produire de nouvelles formes de lamelles, le groupe a développé et industrialisé son propre système de fabrication additive à partir des solutions existantes sur le marché. Depuis 2009, il a mis sous contrôle tous les paramètres pour atteindre la qualité et la répétabilité indispensables à la réalisation en série de pièces de lamelles. Il dispose aujourd’hui d’ateliers dédiés à l’impression métallique fonctionnant 24 h / 24 en environnement industriel, produisant plus d’un million de pièces par an. Cette technologie a permis de concevoir des pneus aux sculptures innovantes, comme le CrossClimate+, premier pneu qui a été certifié pour rouler en conditions hivernales et offrant une adhérence sur la neige similaire à un pneu hiver, et ce pendant toute sa durée de vie.
Des challenges identifiés
La fabrication additive métallique gagne chaque année en maturité, mais elle a encore de nombreux défis à relever. Une des premières difficultés pour les industriels est d’arriver à identifier des exemples concrets de pièces éligibles, que ce soit pour la conception de nouveaux produits ou la production ponctuelle de pièces de rechange. Cette étape nécessite de connaître les possibilités de la technologie, mais aussi ses contraintes. Les règles de conception en fabrication additive sont encore peu connues dans la plupart des bureaux d’études. Et, pour tous les industriels qui ont pris la mesure de l’énorme potentiel de la technologie, il leur reste à inventer les objets imprimés de demain. Car, si aujourd’hui la plupart des applications portent sur des améliorations de performance, rares sont les applications qui tirent pleinement parti de la fabrication additive, en créant des objets totalement nouveaux qui permettent à leurs inventeurs de créer de véritables ruptures sur leurs marchés. Penser en additif et imaginer de nouveaux objets reste le principal défi pour la décennie à venir.
Le deuxième challenge concerne la productivité des machines. Si la fabrication additive a déjà démontré sa pertinence pour un certain nombre d’applications, l’équation économique et les tailles de séries cibles doivent être améliorées pour conquérir des marchés de masse, tels que l’automobile. Les derniers progrès laissent entrevoir des gains de productivité d’un facteur dix pour la seule technologie « fusion sur lit de poudre », à très court terme. Quant aux start-up qui multiplient les annonces portant sur de nouveaux procédés, elles doivent désormais démontrer leur capacité à industrialiser la technologie. Sur ce point, l’émergence d’acteurs à culture industrielle est perçue comme un véritable accélérateur.
Un autre défi est celui des matériaux. La fabrication additive est compatible avec la plupart des alliages métalliques, et les fabricants de machines ont commencé à travailler avec les alliages couramment utilisés dans l’industrie, tels que le titane, l’inconel, l’aluminium, l’acier maraging, l’inox, le cuivre, l’or, etc. Mais il reste une large place pour le développement de nouveaux matériaux, ouvrant la voie vers la production d’objets aux caractéristiques inédites. Partout dans le monde, des laboratoires de recherche travaillent sur des sujets de mise en forme de nouveaux matériaux et de développement de nouveaux types de poudres.
Enfin, il est nécessaire de prendre en compte la problématique HSE (hygiène, sécurité, environnement). Les risques sont déjà connus. Ils sont multiples : risques d’incendies liés à l’utilisation de poudres métalliques très fines (de l’ordre de quelques dizaines de microns) et risques pour la santé, dus à la génération de particules nanométriques pendant la fabrication, dont certaines contiennent des métaux classés CMR (cancérigènes, mutagènes, reprotoxiques). Heureusement, les normes encadrant l’usage des technologies « lit de poudre » seront publiées dans les prochains mois. En outre, certains constructeurs les ont anticipées pour la création de leurs machines et de leurs ateliers. C’est le cas du français AddUp qui, en plus du travail réalisé sur l’étanchéité de ses machines, impose le port d’équipements de protection individuelle (EPI) pour les opérateurs et préconise d’installer les machines dans des zones confinées, à l’atmosphère contrôlée, afin d’éviter toute propagation de la poudre en dehors de la zone de production. Ces règles suffisent à garantir une sécurité totale des utilisateurs et des installations.
“Penser
en additif reste le défi principal.”
Une opportunité pour l’industrie 4.0 et la French Fab
Pour finir, la fabrication additive est un des piliers de l’industrie du futur. Nous avons vu qu’elle permet de créer des objets toujours plus légers, plus performants, plus fiables, et qu’elle donne aux industriels qui l’adoptent la possibilité de prendre une sérieuse avance sur leurs concurrents. Elle permet aussi à de nombreux secteurs d’améliorer, voire de redessiner leur chaîne d’approvisionnement. Les nombreuses initiatives qui ont vu le jour récemment dans le domaine, en raison de la crise sanitaire liée à la Covid-19, démontrent la capacité de la technologie à assurer la fourniture rapide de composants critiques au plus près de leurs lieux d’utilisation.
Les industriels français ont-ils pris le virage de la fabrication additive ? Si les constructeurs allemands et américains sont bien implantés sur le marché de la fourniture de machines (citons General Electric qui a racheté deux leaders du secteur en 2017 pour environ 1,7 milliard d’euros), la filière française n’est pas en reste, avec un écosystème riche et dynamique. La plupart de nos laboratoires participent à des programmes de recherche, dont certains très ambitieux, comme le projet SoFIA (Solutions pour la fabrication industrielle additive) doté de 50 millions d’euros de budget. Des réseaux de recherche se forment dans les différentes régions, telle la plate-forme AFH qui regroupe de nombreux acteurs (AddUp, Air Liquide, EDF, LNE, Onera, Safran, Vallourec, les Instituts Carnot, Cetim, CEA, Arts et Métiers ParisTech, CNRS…) sous l’égide de la région Île-de-France.
Nos écoles s’équipent elles aussi. C’est le cas de l’École polytechnique, qui dispose de moyens de production en DED. Dans le monde industriel, enfin, nos grands groupes se mobilisent et investissent dans la technologie. En 2016, Michelin et Fives ont uni leurs forces pour créer AddUp, fabricant de machines et d’ateliers de production. En parallèle, de nombreuses start-up continuent de se créer, que ce soit dans le domaine du logiciel, de la prestation en conception ou de la fabrication de pièces. Et tous ces investissements s’effectuent avec le soutien actif des pouvoirs publics, à travers l’action de Bpifrance. La fabrication additive est un levier majeur de l’industrie du futur et reste une très belle opportunité à saisir par l’industrie française !
AddUp, joint-venture entre Fives et Michelin
En 2016, les deux groupes Fives et Michelin ont associé leurs compétences, respectivement dans la fabrication de machines industrielles et dans la maîtrise du procédé LBM pour la fabrication de pièces en grandes séries. Ils ont créé la coentreprise AddUp (www.addupsolutions.com) dans le but de proposer une offre complète à destination des industriels, depuis la fourniture de machines et de solutions HSE jusqu’à la livraison d’ateliers complets, en passant par la production de pièces à la demande. Grâce à des acquisitions récentes, notamment le rachat de BeAM (constructeur de machines DED) et une prise de participation majoritaire dans la société Poly-Shape (un des leaders européens de la fabrication de pièces métalliques), AddUp est devenu un fournisseur multitechnologique et dispose d’une capacité de production importante. À cette offre s’ajoute une large palette de services. AddUp accompagne ses clients depuis les débuts de leurs projets, par du conseil et de la formation (www.addup-academy.online), et les aide à toutes les étapes de l’intégration de la technologie : réflexions stratégiques, choix de la technologie, identification des pièces éligibles, aide à la reconception de pièces, réalisation de preuves de concept, développement de recettes, optimisation des paramètres de production, etc.
Pour en savoir plus sur la fabrication additive métallique : www.addupsolutions.com et www.addup-academy.online