4D Pioneers, une start-up en impression 3D issue de la recherche



Les matériaux disponibles pour l’impression de pièces en 3D sont de plus en plus variés et techniques. Mais, pour répondre aux contraintes industrielles, encore faut-il que ces pièces soient suffisamment performantes pour être durables. Cette question définit un chantier spécifique de recherche.
Les matériaux conçus par impression 3D, qu’ils soient organiques ou minéraux, sont en pleine expansion. Ils sont très utiles pour la mise au point de prototypes avant un usinage « en dur », mais ils semblent quitter ce domaine restreint pour être employés dans la fabrication de pièces fonctionnelles. Ces pièces peuvent, dans un premier temps, être destinées à remplacer des éléments usés ou hors d’usage d’un ensemble plus complexe. Cet emploi, qui peut aller de petites machines domestiques à des systèmes industriels, est économiquement intéressant pour des raisons évidentes. Il l’est aussi sur l’aspect environnemental car il évite le remplacement total de la structure à laquelle la pièce appartient. L’environnement de la pièce remplacée peut lui imposer de nombreuses sollicitations : mécaniques, thermiques, hydriques, etc. Ce sont ces sollicitations qui vont définir les nécessaires critères de durabilité que devra remplir la pièce pour maintenir ses fonctions « le plus longtemps possible ». Le problème posé est complexe, car la structure réalisée par impression 3D dépend non seulement du matériau utilisé mais aussi des conditions d’impression (densité, remplissage, ajouts…).
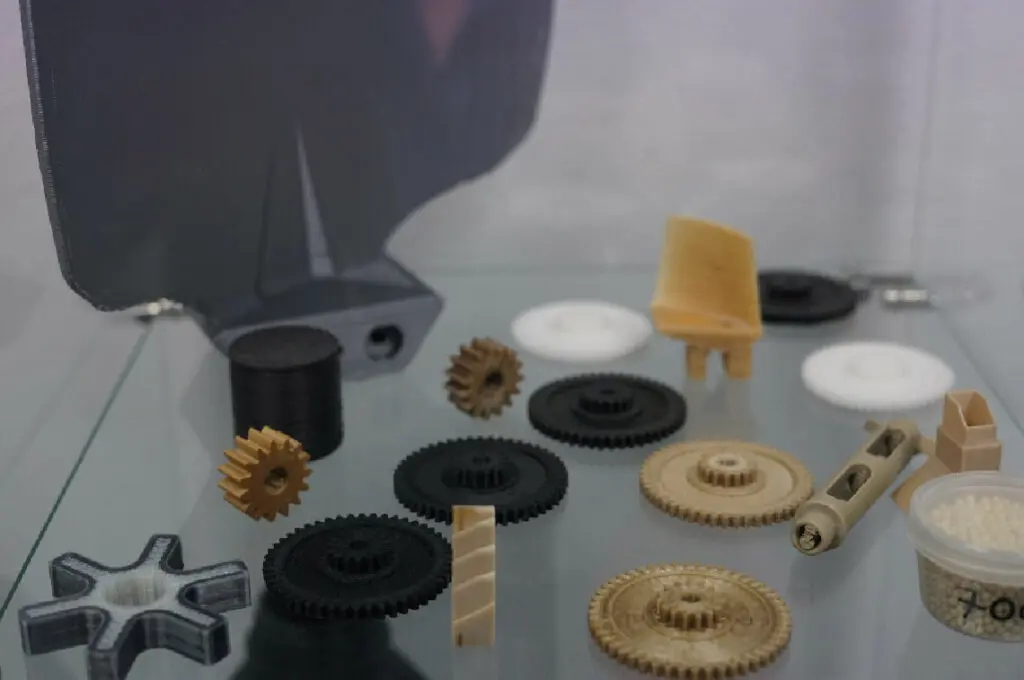
De nombreux matériaux possibles
Si l’acier constitue une part fondamentale des pièces dans l’industrie, la recherche d’autres matières s’accélère, que ce soient d’autres métaux ou la céramique, les polymères, ou encore les composites. Les céramiques font l’objet de ces nouvelles approches. Elles ont l’avantage d’avoir d’excellentes performances mécaniques et aussi une très bonne stabilité au feu, et elles sont chimiquement inertes. De plus, c’est un matériau isolant très adapté à de nombreux cas industriels où la température est un problème clef. De récentes innovations ont vu également le jour dans les polymères, tels que les néomatériaux également appelés thermoplastiques hautes performances. On peut par exemple parler du PEEK (PolyÉtherÉtherKetone) qui fait partie des polymères à hautes performances et dont les propriétés sont parfois supérieures à celles des métaux classiques. Ce sont d’excellents candidats pour la fabrication de pièces dont l’environnement est agressif (radiologie, agressions chimiques, température, etc.).
La transition du métal vers les composites est une mutation culturelle profonde pour la mécanique, nécessaire pour apporter notamment des solutions d’allègement, en réponse aux exigences de consommation énergétique ou environnementales – réalisation avec moins de matière, moins de rejets et une moindre consommation, sans compromettre les performances. Il existe, pour certains équipements industriels, des pièces (servomoteurs électriques, engrenages – parfois bimatières en acier et plastique) qui permettent le bon fonctionnement de l’appareillage mais qui sont très souvent conçues pour une application particulière. Afin d’optimiser le processus de maintenance et d’obtenir de meilleures propriétés, il est intéressant de remplacer ces pièces par des éléments monomatières mais dont les performances seront augmentées. Ces pièces étant atypiques et uniques, seule l’impression 3D permet de répondre rapidement et efficacement à ce besoin. Par exemple il est possible d’imprimer des engrenages avec des thermoplastiques à hautes performances, tels que des polymères techniques ou tout autre matériau de même nature.
“En mécanique
le passage du métal aux composites constitue
une mutation culturelle.”
Une stratégie d’impression liée au vieillissement
L’exploitation plein potentiel de l’impression 3D passe par une maturité avancée : connaissance des possibilités offertes dès la conception et évaluation de la durabilité du matériau imprimé. L’idée est d’enrichir et de compléter une approche qui serait limitée à la seule mécanique. La pièce imprimée sera poreuse. L’impression par couches, avec un taux de remplissage inférieur à un, va générer une structure contenant des vides dont le volume quantifiera la porosité. Bien souvent ces vides sont connectés. Cette structuration donne au matériau imprimé une perméabilité qui traduit l’aptitude du milieu à se laisser traverser par un fluide sous gradient de pression. Cette propriété peut être vue comme une propriété cible, dont on chercherait une valeur minimale pour une pièce devant répondre à des conditions d’étanchéité.
La porosité est aussi le lieu des échanges de fluide avec le milieu extérieur, elle représente alors une surface de contact importante qui apparaît comme une vulnérabilité si les fluides sont agressifs. La dégradation mécanique est, pour beaucoup de matériaux, liée à une fissuration progressive qui va diminuer leurs performances. La perméabilité, en particulier au gaz, est très sensible à la fissuration, on peut ainsi en faire un outil de détection très fin. Porosité et perméabilité peuvent être couplées avec d’autres types de mesures plus techniques (poromécaniques par exemple) et devenir des outils novateurs pour évaluer la qualité du matériau imprimé 3D, initiale ou après dégradation.
Un centre de recherche novateur
Une connaissance approfondie des différents matériaux (physique, mécanique, porosité et vieillissement des matériaux) et une maîtrise des stratégies d’impression 3D sont donc essentielles pour le développement de nouvelles pièces fonctionnelles. Pour y répondre et soutenir l’innovation industrielle, trois laboratoires de pointe (laboratoire de mécanique, multiphysique, multiéchelle à Centrale Lille ; laboratoire procédés et ingénierie en mécanique et matériaux à l’Ensam Paris ; centre de recherche de l’industrie belge de la céramique au BCRC Mons) ont réuni leurs compétences pour la création d’une nouvelle entité de service sous le nom de « 4D Pioneers ».
4D Pioneers apporte aux industriels un service à 360° englobant : l’analyse de l’environnement de la pièce et l’élaboration du cahier des charges, l’élaboration de son design, des recommandations sur les matériaux les plus adaptés, la sélection du processus d’impression 3D, la production des pièces via son hub technologique (alliages, polymères ou céramiques) et la quantification de la durabilité en conditions in situ. Par ce service, 4D Pioneers souhaite révolutionner les pratiques industrielles en matière d’obsolescence en démontrant que la 3D est une solution particulièrement efficace pour prolonger la durée de vie des structures en remplaçant des pièces obsolètes ou fonctionnelles par des éléments conçus avec des matériaux plus performants au design optimisé.